四方科技主要從事食品冷凍裝置制造,以往產(chǎn)品的機架及結(jié)構(gòu)件主要以管型材拼接為主。鈑金件由于具有敞開的形式,制造工藝簡單,制造效率高等特點,逐步在食品機械的機架及結(jié)構(gòu)件中得到應(yīng)用,并且成為一種行業(yè)趨勢。中板鈑金廣泛運用在該領(lǐng)域,但中厚板受材料厚度、折彎工藝、焊接工序等的影響很大,通常會在成形后出現(xiàn)缺口相對較大的現(xiàn)象,導(dǎo)致焊接變形隨之增大,從而無法保證零件的尺寸和形位公差,甚至焊接的缺陷給產(chǎn)品的外觀質(zhì)量帶來致命影響。其次中厚板加工具有一些工藝難點,為克服工藝難點,我公司鈑金工藝人員總結(jié)了一套行之有效的方法,解決了中厚板鈑金加工問題,在此與大家分享。
中板鈑金工藝分析
首先來看實例,圖1為我公司某產(chǎn)品的固定支架,材料是拉絲SUS304,厚度為4mm,接下來,我們討論它是如何實現(xiàn)精密加工的。
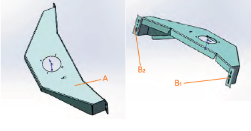
圖1 產(chǎn)品固定支架
零件質(zhì)量要求分析
⑴首先保證基準面A的平整度以及面A與面B1、B2的垂直度,是滿足裝配形位關(guān)系,保證機器位置精度的關(guān)鍵。⑵強調(diào)折彎的精度,需要保證B1、B2面的橫向尺寸和固定支架隱含的相對尺寸,以及產(chǎn)品的尺寸精度關(guān)系。⑶形位精度和尺寸精度與下料、校平、折彎、焊接等工藝息息相關(guān)。⑴鈑金工序控制主要強調(diào)工序的正確性,該零件合理的鈑金工藝流程是:原材料(平整度較好的拉絲板)→激光切割→校平→折彎工序(關(guān)鍵工序控制)→焊接。1)傳統(tǒng)的工藝是采用SolidWorks畫法,正常展開、折彎、焊接,結(jié)果發(fā)現(xiàn)零件縫隙很大,焊接時填絲量很大,大家都知道不銹鋼焊接后變形會更大,從而導(dǎo)致零件焊接后變形無法控制,根本無法生產(chǎn)出滿足裝配精度要求的合格品,零件縫隙如圖2所示。
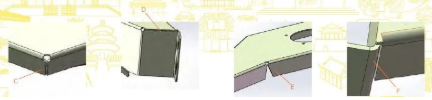
(a)C處最大縫隙為4mm(b)D處最大縫隙為0.8mm (c)E處選擇三角形補塊填充(d) F處最大縫隙為2mm
圖2 零件折彎后縫隙
2)我們的做法是用畫圖軟件展開此零件,在C、E、F處加薄片,將焊接后的最大縫隙控制在0.2~0.3mm,在鈑金折彎前用手動倒角機或拋光機去除多余的基材,從而實現(xiàn)零件的精密加工。如圖3所示紅色圓圈所示。

(a)添加薄片2mm×52mm并倒角3.5mm×22°,折彎后狀態(tài) (b)添加薄片0.7mm×121.5mm, 折彎后狀態(tài) (c) 添加薄片2mm×56mm并倒角 3.5mm×20°,折彎后狀態(tài)
圖3 零件縫隙消除措施
1)零件工藝圓孔要大一點,在食品機械行業(yè)是不需焊接的,反而更有利機器的清潔。2)使用三維柔性平臺保證工件的形位與尺寸精度,用氬弧焊打多點粘接焊接部位,待工件固定后,可以拿下零件,完成自由焊接,可有效節(jié)省時間。3)焊接時,由于產(chǎn)品縫隙很小,可以不用加焊絲,而是采用自熔方式,焊接后紋理漂亮,無需打磨,不但提高效率和產(chǎn)品的表面質(zhì)量,更為關(guān)鍵的是焊接小間隙零件不產(chǎn)生收縮,零件基本上無變形,無需增加整形工序,可一次性滿足技術(shù)要求。
中厚板鈑金工藝分析
在結(jié)構(gòu)設(shè)計中經(jīng)常會遇到折彎R角與不同材料厚度連接的焊接方式,由于R值較大,焊接填料很多,會產(chǎn)生較大熱量及收縮變形,一般通過修改零件結(jié)構(gòu)的方式,如把直角焊接改成平面對接的方式焊接,完成中厚板精密加工,如圖4所示。
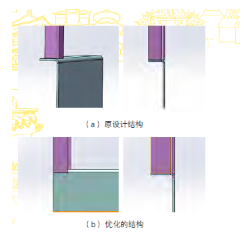
圖4 結(jié)構(gòu)優(yōu)化對比
結(jié)構(gòu)優(yōu)劣對比:優(yōu)化后容易實現(xiàn)焊接,焊接變形小,無需打磨工序,外觀面平整、美觀,提高效率,節(jié)省成本。中厚板焊接工藝同樣可以通過鈑金折彎工藝來實現(xiàn)。板厚8mm,材料為雙面拉絲SUS304,原設(shè)計需要焊接側(cè)板,改變結(jié)構(gòu)后變焊接為折彎,如圖5所示。
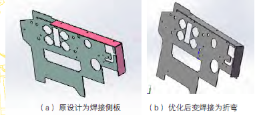
圖5 中厚板工藝改進
2)實現(xiàn)鈑金結(jié)構(gòu)件后,要注意細節(jié)方面的處理,如焊接時,R角過渡相對較小,比較美觀,而8mm板材鈑金折彎R角太大,折彎噸位也大,所以我們經(jīng)過有限元強度分析后做改善處理,見圖6。
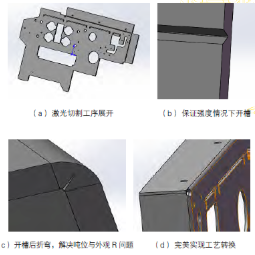
圖6 優(yōu)化后的零件
結(jié)束語
以上工藝在公司新產(chǎn)品開發(fā)中已廣泛使用且成果斐然,我公司的技術(shù)工藝和加工方式明顯超越同行,解決了中厚板鈑金精密加工的難題。誠然,還需要鈑金行業(yè)與其他相關(guān)行業(yè)從業(yè)人員共同努力,推動技術(shù)廣泛使用,同時總結(jié)出更優(yōu)質(zhì)的問題解決方案,推動鈑金中厚板加工工藝的繼續(xù)進步。